In my 28 years of fire sprinkler experience, I’ve seen countless situations where a minor repair or scheduled maintenance could have prevented a massive and costly repair—if not a catastrophic failure or, even worse, a life-threatening situation. Fire sprinkler systems are incredibly effective, but like any mechanical system, they require routine upkeep to function properly when they’re needed most. Best practices for fire sprinkler maintenance involve regular inspections and testing, as well as being proactive about addressing small issues before they become major problems.
Fire sprinkler systems aren’t “set it and forget it” safety measures. They rely on multiple components working together, and if one fails, the entire system can be compromised. Routine inspections and fire sprinkler testing are critical to ensuring your system functions properly in an emergency.
Wet and Dry Systems: Unique Challenges
Wet sprinkler systems are the most common and, on the surface, the simplest type. However, that doesn’t mean they’re maintenance-free. Valves can fail to open when needed, water supplies can be unknowingly shut off, and drains can become clogged, leading to system failures. Even notification devices like water motor gongs can become nesting spots for birds and insects, rendering them useless when an activation occurs. A system that appears to be in working order might have hidden issues that only routine inspections can uncover. Common fire sprinkler system maintenance mistakes include overlooking small signs of failure, which can lead to catastrophic consequences down the road.
Dry sprinkler systems present their own set of challenges. Unlike wet systems, they rely on air pressure to keep water out of the pipes until activation. These systems incorporate air compressors, which require regular maintenance, including checking filters, oil levels, belts, and condensation drains. Over time, condensation can accumulate in low points of the piping, leading to internal corrosion. This corrosion can partially or even fully block pipes and sprinkler heads, rendering the system ineffective when it’s needed most. Without scheduled inspections, these issues can go unnoticed until it’s too late. How to prevent fire sprinkler system failures? Stay on top of these routine checks, and make sure your system is tested and maintained regularly.
Fire Pumps: The Heart of the System
If a sprinkler system is the backbone of fire protection, then the fire pump is the heart, ensuring water gets where it needs to go with the necessary pressure. Whether powered by an electric motor or a diesel engine, fire pumps must be inspected regularly by a qualified professional. These pumps should be churned weekly or monthly, but more importantly, they must be tested under real operating conditions to confirm they’re functioning properly. This testing should be part of a broader plan of NFPA 25 compliance for fire sprinkler systems, ensuring the safety of your building and occupants.
A seemingly small oversight can have disastrous consequences. Take, for example, a building technician performing a monthly churn on a fire pump but failing to check the discharge of the casing relief valve. If the drain isn’t clear and capable of handling the pump’s flow, water can back up into the room. This might not seem critical—until that same pump runs overnight with a malfunctioning alarm signal, and no one is alerted. In one instance, this led to an entire switchgear room flooding with two feet of water, stopping just inches away from a 13,200-volt electrical supply line powering the entire building. All of this occurred simply because a floor drain was clogged.
On the flip side, some building technicians will close relief valves altogether to prevent water discharge, unaware that this can create another major issue. If the fire pump runs without the casing relief valve functioning properly, excessive pressure/temperatures can cause severe damage to the rotating assembly, leading to total pump failure. In some cases, this has required complete pump replacements—an expensive and entirely preventable repair. When it comes to your building’s Life Safety systems, it’s best to leave it up to the professionals, especially those providing fire sprinkler testing and maintenance services.
Fire Sprinkler Systems: A Proven Lifesaver
Fire sprinkler systems have been around for over 150 years, proving time and again that they are the most effective way to protect both people and property from fire. However, they are not immune to neglect. Routine maintenance isn’t just a recommendation—it’s a necessity.
By staying proactive with inspections, testing, and preventative maintenance, you can ensure that your fire sprinkler system is always ready to perform when needed. Don’t wait for an emergency to discover an issue that could have been easily fixed beforehand. Fire sprinkler system maintenance services aren’t just about compliance—they’re about peace of mind, knowing that your building’s fire protection systems will work when it matters most.
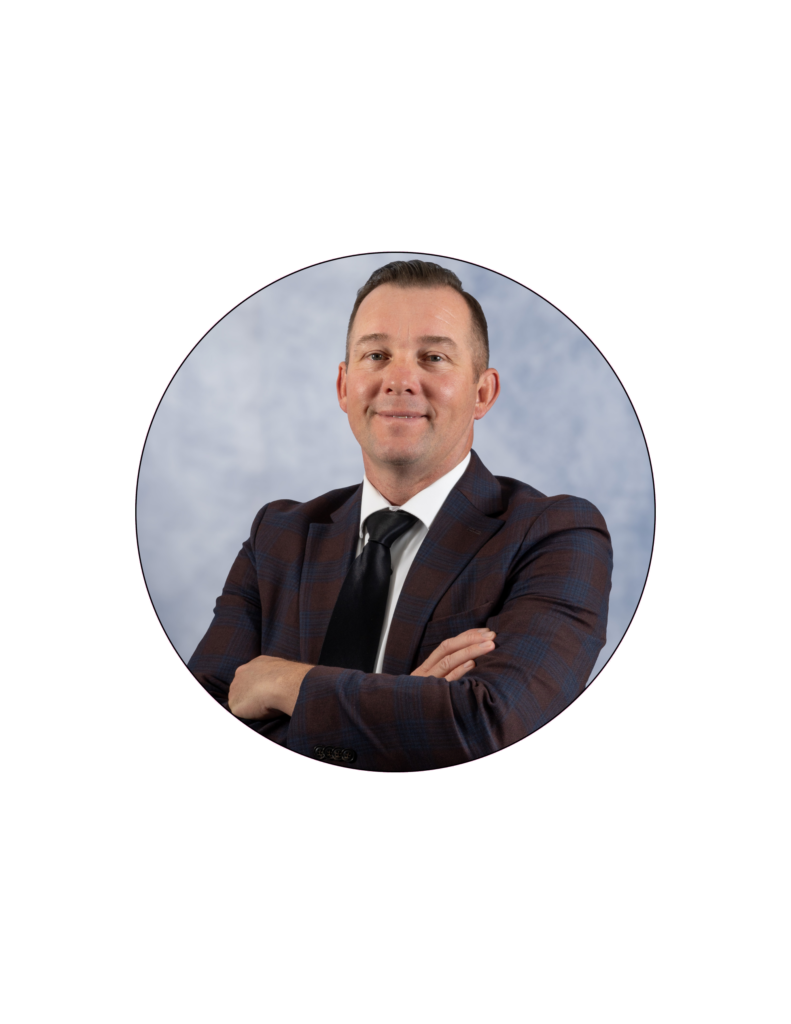
Article by Pat Doyle
Director of Business Development